Så tillverkas arbetsskorna steg för steg – levererar 100 000 par om året
Sveriges största fabrik för skyddsskor levererar 100 000 par skor per år. Byggnadsarbetarens fotograf Tom M Kronestedt följde tillverkningen av den senaste modellen – Örebro.
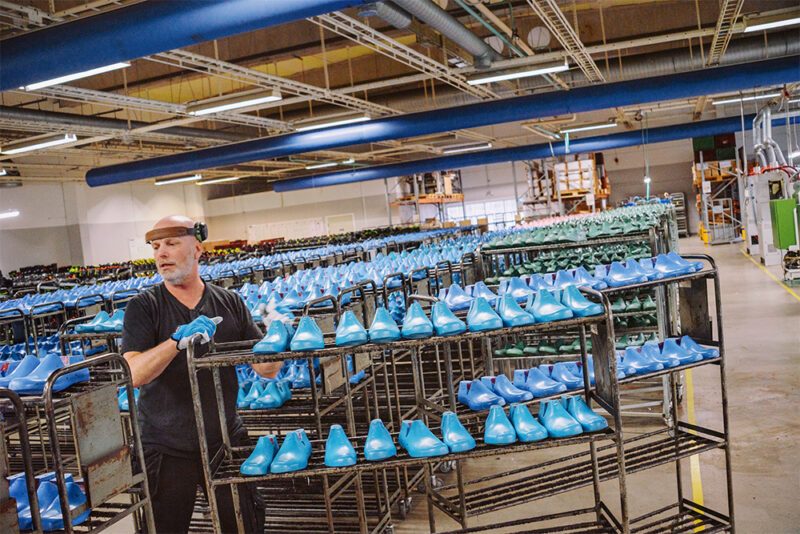
I Kumla har det tillverkats arbetsskor i snart 200 år. Allt börjar 1839 när den blott 18-årige Anders Andersson beslutar sig för att tillverka så många exemplar han kan av samma modell, i stället för att skräddarsy varje par när kunden beställer. Den svenska partiskohandeln är född.
1946 reser sonsonen Helmer till USA. Med sig hem har han en innovation – stålhättan. Två år senare släpper Arbesko sin första moderna skyddssko. Företaget är fortfarande familjeägt och produktionen finns alltjämt i Kumla.
- Färdigsydda ovandelar i läder levereras till Kumla från Arbeskos fabrik i Brasilien.
- Bindsulan, skons stomme, fästs i lästen med klammer. Lästen är den form som skon tillverkas på.
- Bakkappan i termoplast formas runt lästen.
- Skyddskappan limmas fast mellan ovandelens två lager.
- Runt tåpartiet viks ovandelen ned och limmas fast. Ovandelen nitas fast i hälen med spik.
- Lästen tas ur och skon förbereds för sulning.
- Yttersulan gjuts på skon.
- Restmaterial skärs bort och alla skor inspekteras för hand. Nu får skon sin innersula.
- l Skorna läggs i en kartong och skickas till centrallagret i Ulricehamn.
Det är aldrig tyst i Arbeskos fabrik. Maskinerna väser, pyser, surrar och slamrar. Precis som på 1800-talet är skornas huvudsyfte att skydda. Men utvecklingen har gått framåt sedan dess. I dag är tillverkningen en teknisk historia.
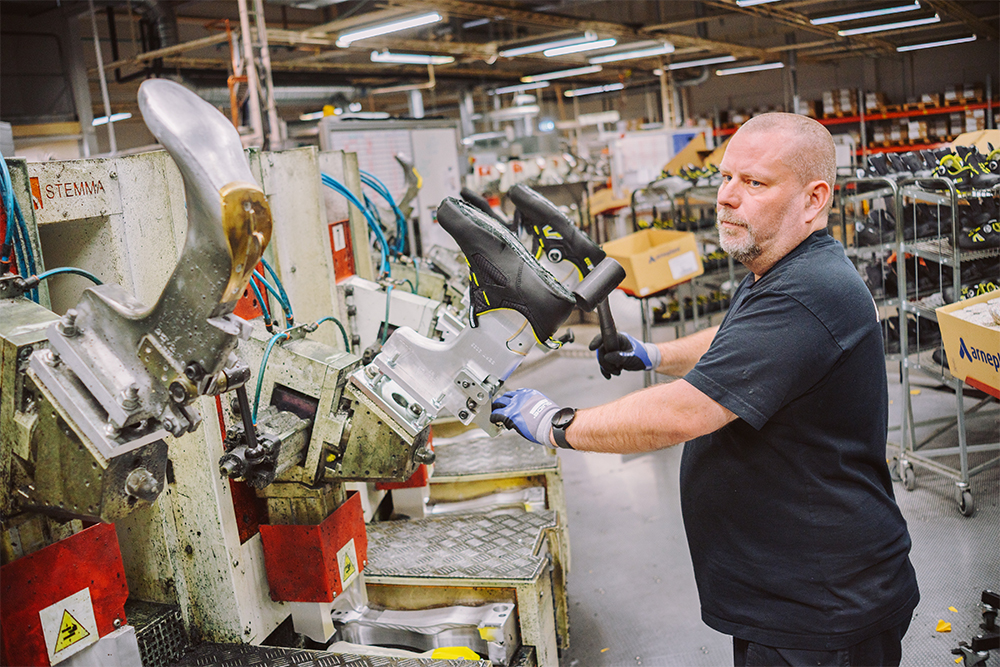
KÄNSLIGA PROPORTIONER. Mellansulorna tillverkas av plastmaterialet polyuretan, en mångsidig tvåkomponentsprodukt som består av polyol och isocyanat. Proportionerna är känsliga. ”Jag ska tillsätta 20 gram vatten till 200 000 gram polyol. Tar jag 30 gram eller 10 gram blir det fel densitet på sulan”, förklarar maskinoperatören Johan Karlsson som att det vore den naturligaste sak i världen.
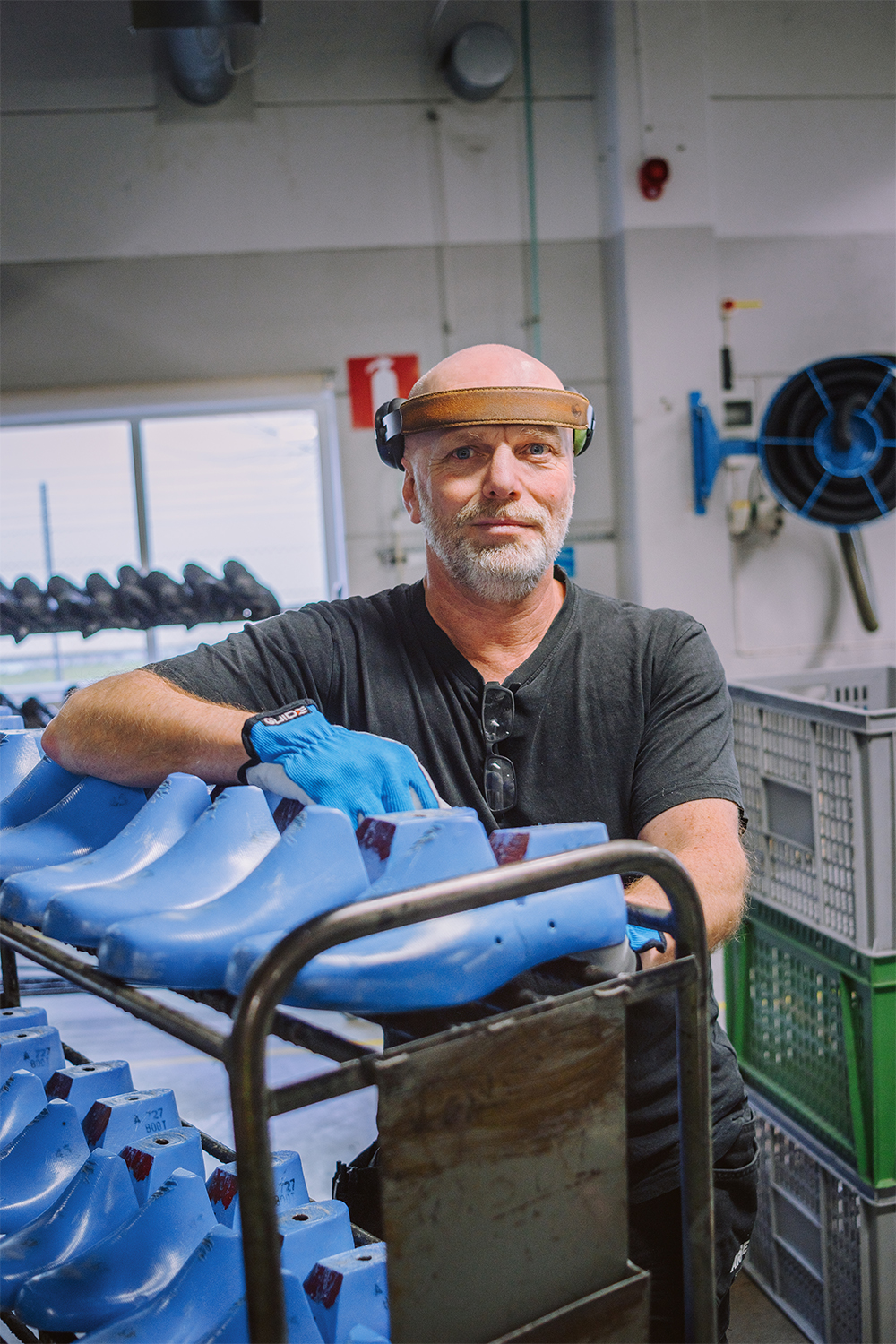
30 ÅR I KUMLA. Tord Engström började sin yrkesbana som grovplåtslagare. Det var långa resor, långa dagar och långa helger. Tord trivdes, men när barnen kom behövdes fastare tider. 1994 tog han anställning på Arbesko.
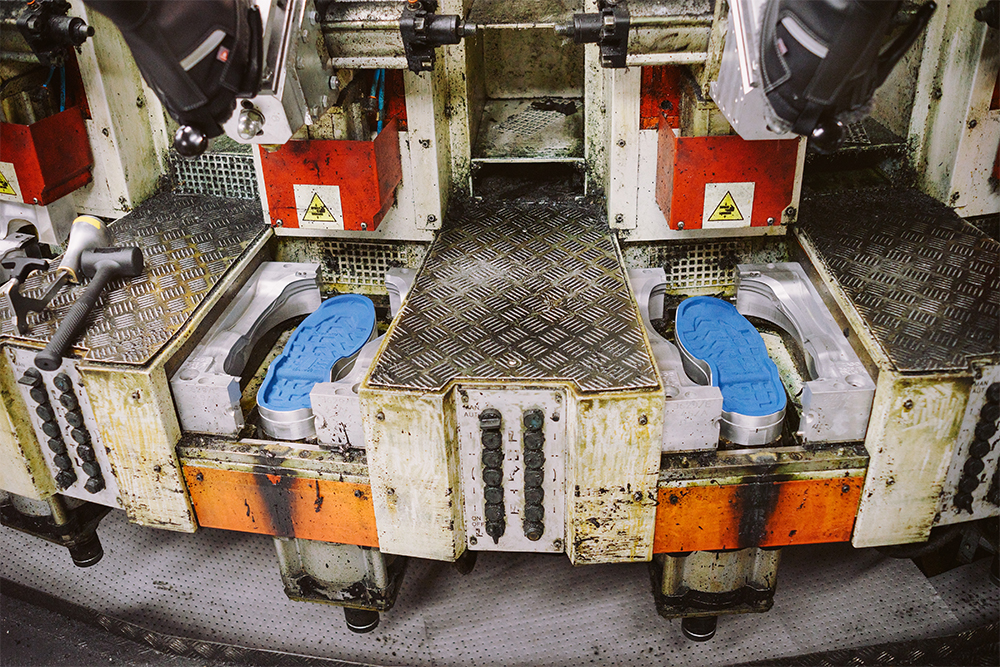
ROBOTJOBB. Maskinen tillverkar en sula i minuten. Totalt 1 200 sulor per dag. En robot från ABB ruggar upp skons undersida innan den pressas samman med sulan.
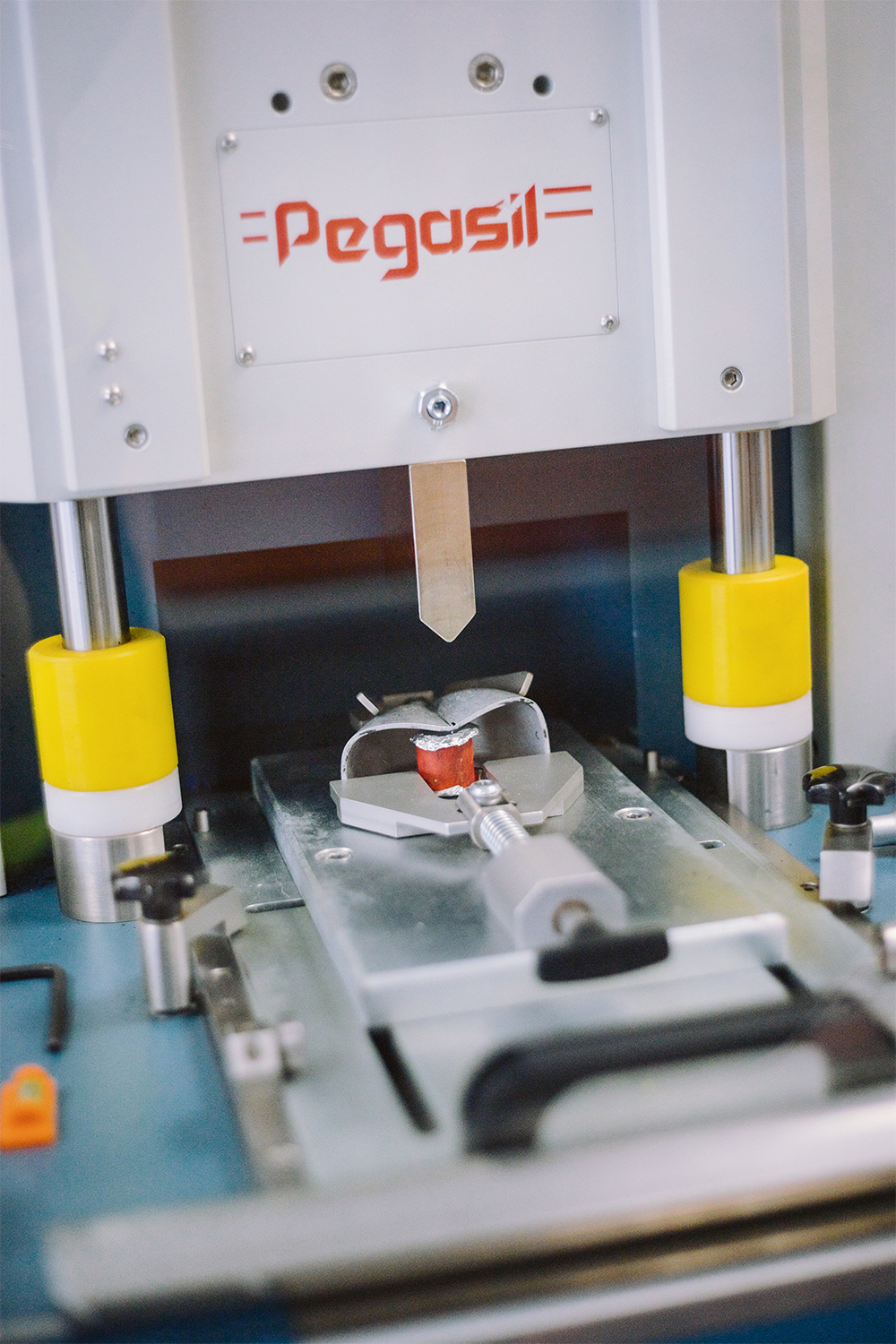
HÄTTORNA TESTAS. Tidigare tillverkades skyddskapporna i stål, men nu används mest aluminium får att få lättare skor. Nästa steg i utvecklingen väntas bli kappor av kolfiber. Maskinen som testar skyddet utsätter hättorna för en kraft på 200 joule. Det motsvarar ungefär 20 kilo som faller från en meters höjd.
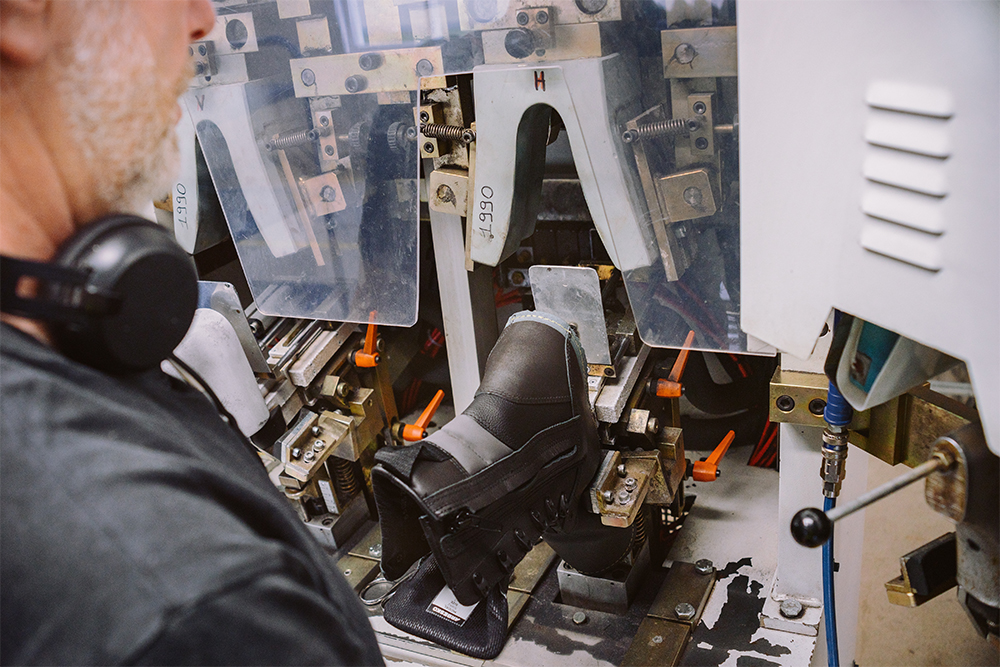
FORMEN FIXERAS. Här formas bakkappan som ger stöd för hälen. Först hettas materialet upp till 150 grader. Sedan kyls bakkappan till minus fem grader för att fixeras i sin form.
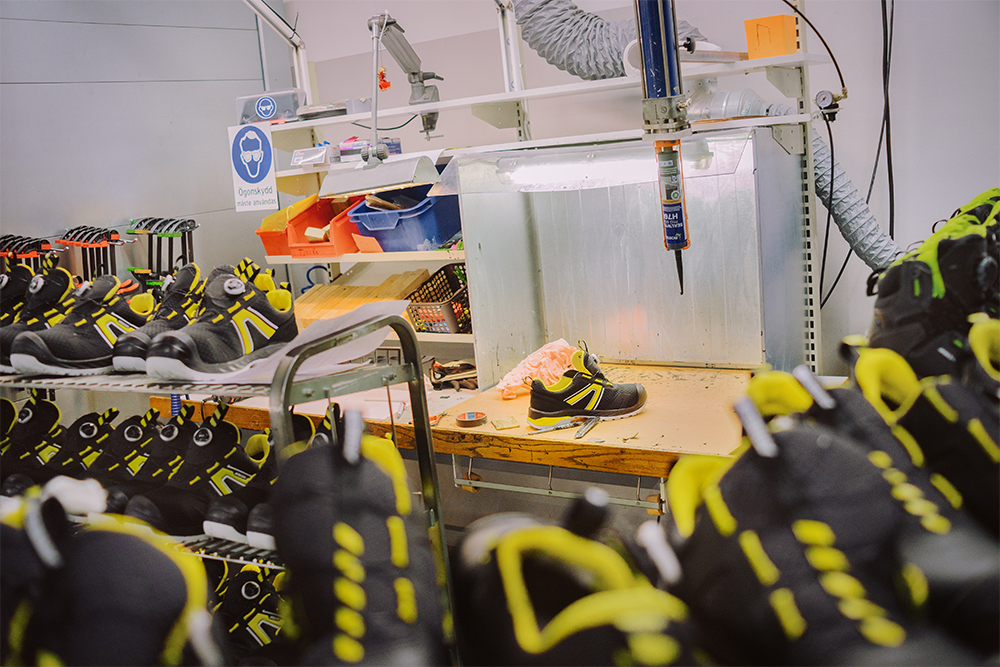
DÖPTA EFTER ORTER. Vad har Umeå, Kiruna, Bredsjö, Oxelösund och Svartå gemensamt? Samtliga är orter som fått ge namn åt Arbeskos olika modeller. Här syns det senaste tillskottet Örebro, en ”smidig och luftig skyddssko med utmärkt grepp”.
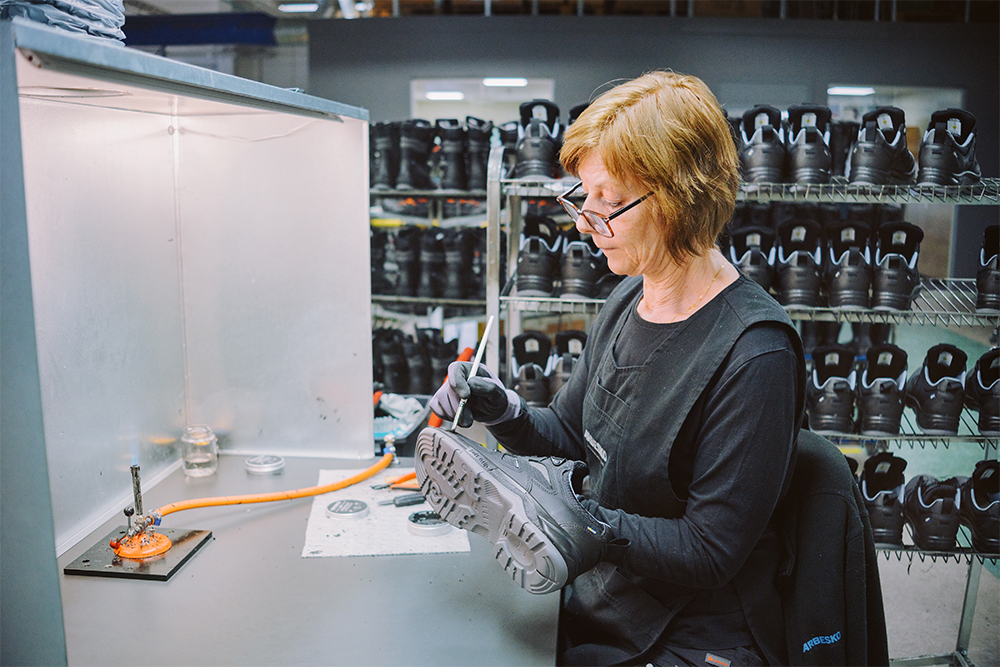
LETAR SKADOR. I puts- och packavdelningen kollar Yvonne Nilsson skorna en sista gång. Letar efter skador och ojämnheter. Målar på extra färg där det behövs och bränner bort lösa trådar. 40 år har det blivit på Arbesko. ”Jag har trivts väldigt bra. Visst blir det enformigt, men jag får röra på mig.”
LÄS MER:
Så säkra är de trendiga skyddsskorna: ”Hänt otroligt mycket”
Få de senaste byggnyheterna – direkt i din inbox! Prenumerera på Byggnadsarbetarens nyhetsbrev.